Brewing on Display: Where Brand & Manufacturing Meet
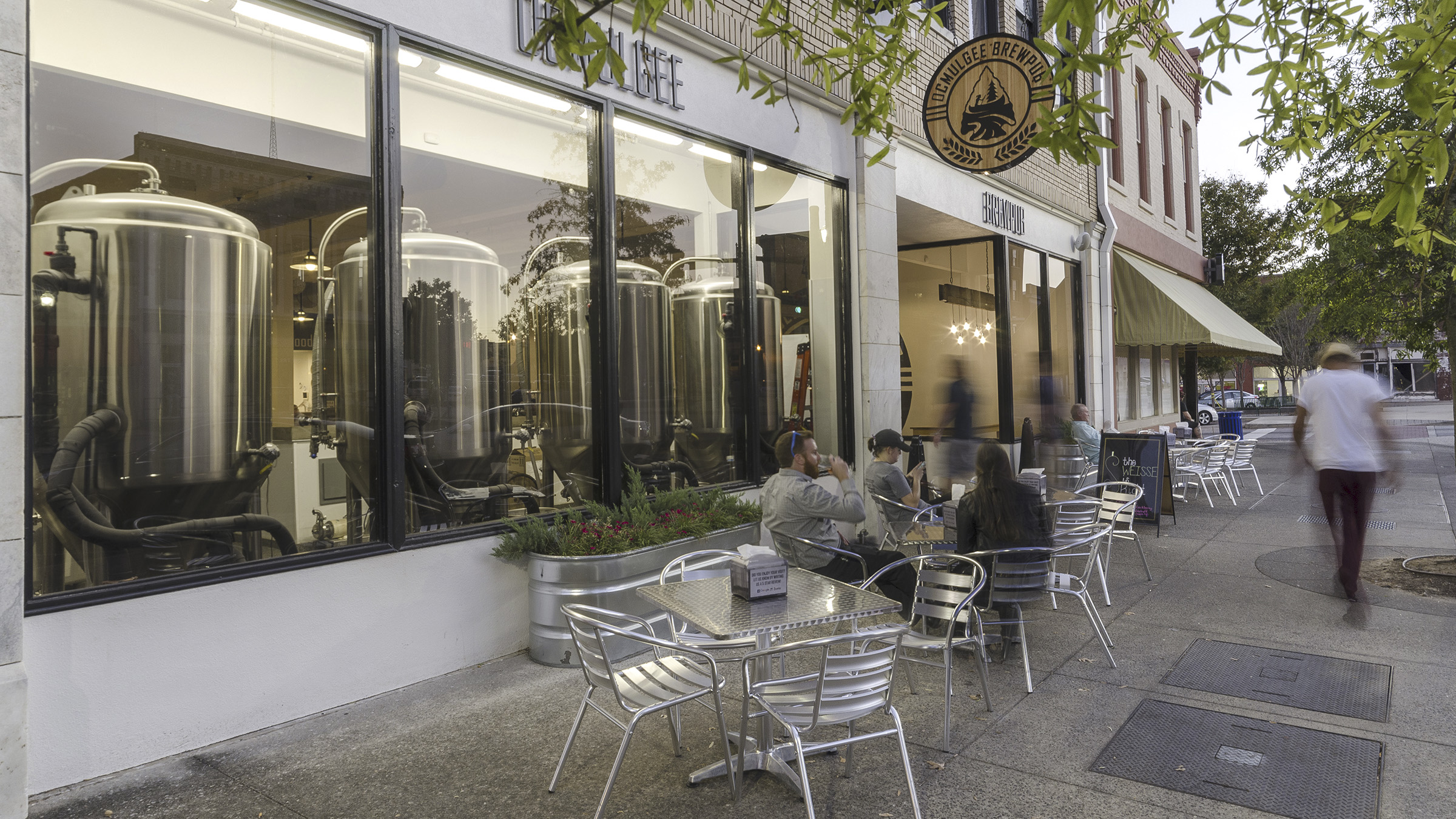
Brewing tanks on display at Ocmulgee Brewpub in Macon, Georgia
With the explosion of the craft beer industry across the United States, cities and towns of all sizes are benefitting socially and economically from the establishment of local breweries. Ocmulgee Brewpub makes its mark in Macon, GA, a city known for its industrial and manufacturing industry and being a transit hub smack in the middle of the state. Named for the wide, deep river that runs through Macon, the brewery’s design melds the importance of brand and the customer experience with the technicalities of food grade engineering.
JBK Southern, Inc. came to Clark Nexsen’s Commercial Practice with a unique set of challenges and goals: to create a design scheme reminiscent of European style beer gardens, put the brewing process on display, and maximize square footage – while meeting an aggressive budget and timeline. A familiar tale in the manufacturing industry, time is money, meaning that a fast track design and construction schedule was critical to get this brewpub operational. Working closely together, the team and client evaluated each element of the design in terms of workflow, impact to the budget, and speed of installation.
Central to the brewpub’s brand is the concept of operational transparency, with the brewing process displayed prominently in wide storefront windows – visible to patrons outside and within.
The emphasis on showcasing the brewing process impacted both the architectural programming of the space as well as the process engineering. The resulting system flows from the millhouse, to the brewhouse and fermenters in the storefront, and ultimately to bright tanks located in a large cooler in the basement, from which the fresh beer is piped up to taps.
The brewing system encompasses multiple floors and locations throughout the building, and the process is by turns complex and surprisingly manual. Located in the basement below the brewhouse, the boiler forces steam up to produce the hot water necessary to begin the brewing process in the mash tun and kettle. During the boiler’s installation, our team provided a rapid response to our client’s call for help: for a reason the installers couldn’t determine, the entire system kept filling with water, never producing steam, and time was of the essence. While the solution ended up being very simple – the solenoid valve had been installed backward, effectively allowing city water to continuously flow into the system rather than managing the flow as needed – having the ability to quickly react and resolve such issues in person is invaluable in the manufacturing setting.
From the kettle, the wort (as beer is known at this stage) is transferred to the stainless steel fermenters, which feature glycol jackets to rapidly cool the liquid, allowing yeast to be added for the fermentation process. In addition to providing the mechanical engineering documents to guide installation, connections, and routing, our design integrated a panel through which the brewmaster can program the temperature for each individual fermenter – allowing him to customize based on the type or style of the beer. When fermentation is complete, a sanitary hose is used to transfer the beer to the bright tanks in the basement where the beer will complete its carbonation, remain chilled, and be ready to serve to customers.
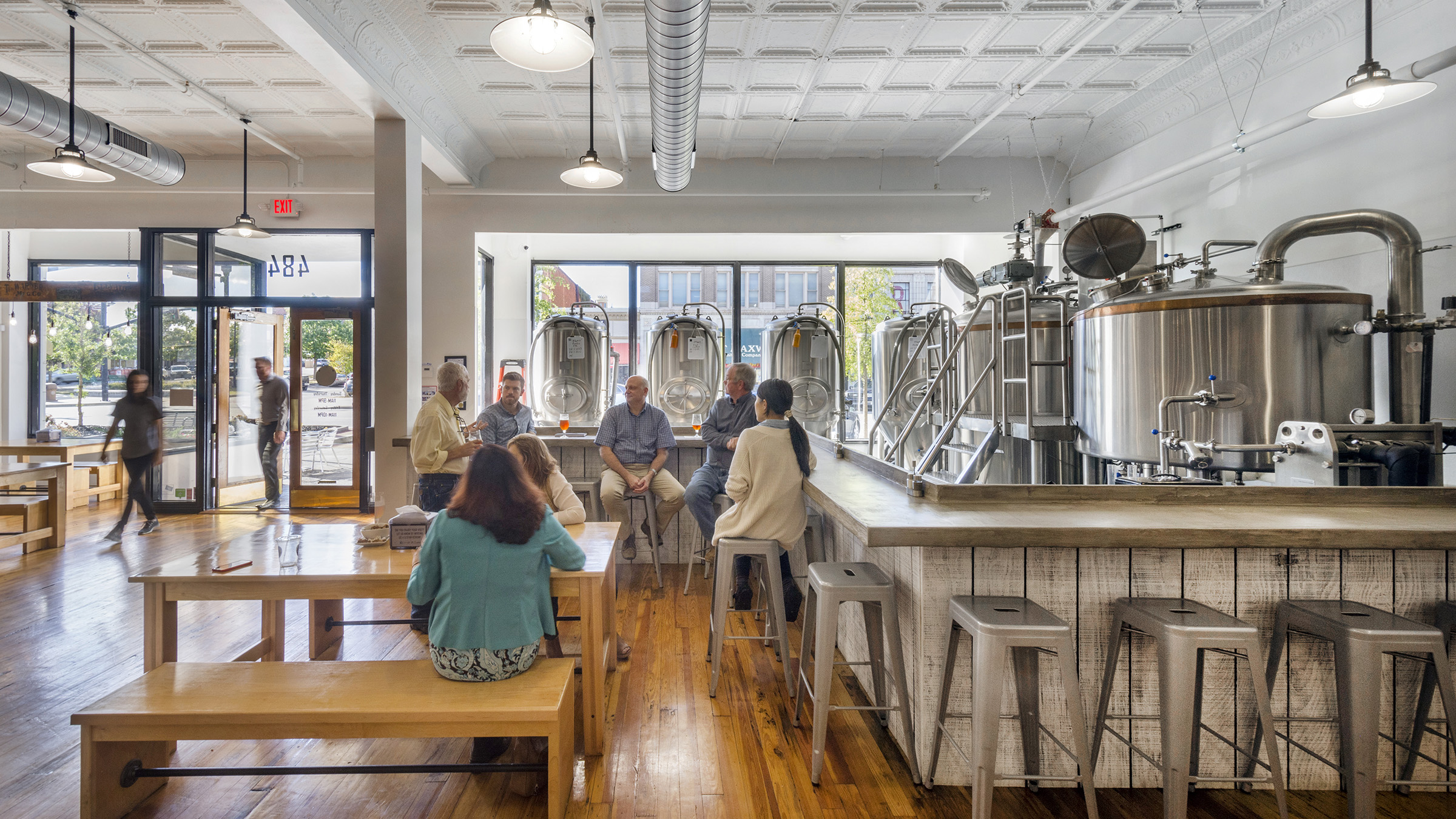
Involving food grade specifications, components like the sanitary hose and pump must be cleaned after each beer transfer and can be used to connect each fermenter to each bright tank – a more manual, and also more cost effective, approach than running repetitive pipes between each. Like many manufacturing clients, JBK Southern, Inc. knew their process and how each component worked together but needed support defining and detailing that process. Our role was to devise the plan that made the brewing process possible, creating drawings that provided technical information regarding connections and sizing, material specifications, routing, and equipment location.
The flow of the entire facility was informed by how Ocmulgee brews beer and serves food, with circulation from the entry focused on the brewhouse visual and quick access to the bar. Throughout the programming stage, the team worked to consider all aspects of both the customer experience and the work flow for employees, evaluating opportunities to improve efficiency and optimize the limited square footage. Today, the brewpub’s communal-style tables, clean industrial aesthetic, and branded design promote new connections and reinforce its sense of place – representing how brand and manufacturing can meet in the commercial environment.
Wade Williams, PE, LEED AP BD+C leads the mechanical engineering department in the Macon, GA office. His experience spans commercial, healthcare, federal, state, and higher education projects. To learn more about the mechanical and process design of Ocmulgee Brewpub or to discuss our engineering capabilities, please call 478.743.8415 or email wwilliams@clarknexsen.com.