Designing A Successful Engineering Building: A Case Study of Fitts-Woolard Hall
Higher education engineering programs span a diverse range of studies, each with unique requirements and activities in their lab spaces. In the following, Clark Nexsen mechanical engineer Adam McElhaney highlights how various laboratories in NC State’s Fitts-Woolard Hall required a complex web of engineering systems to support their functionality.
Completed in 2020, working on the 225,000 square feet Fitts-Woolard Hall was incredibly unique because it has various laboratories, such as a structural testing lab, a large-scale driving simulator, computational labs, and education and research labs. Moreover, the building puts the research and instruction “on display,” with views into lab and classroom spaces from the exterior and interior of the building, helping foster curiosity, interaction, and problem-solving between the different engineering disciplines housed within Fitts-Woolard Hall.
Laboratory buildings for commercial and educational projects usually focus on one or two disciplines rather than the various lab types that Fitts-Woolard called for. From a mechanical design perspective, one of the critical things we need to solve when working on lab buildings is figuring out the lab requirements from a ventilation and load perspective. We start this process by collaborating with the owner and lab planner to classify the space. Different classifications of labs trigger different requirements – what are the air change requirements? Is recirculation permitted, or is the space required to be served by a single pass, 100% outdoor air system?
The lab classification can also inform the type of energy recovery that can be utilized if any exhaust air filtration or treatment is required, the duct materials, and whether there are any redundancy or continuous operation requirements for the HVAC equipment. Next, we need to understand the load density requirements – how many people will be in the lab? Which pieces of lab equipment will generate heat? How much diversity should be considered? Since Fitts-Woolard Hall has so many different types of labs, we went through each one to understand their variations and the systems needed for support.
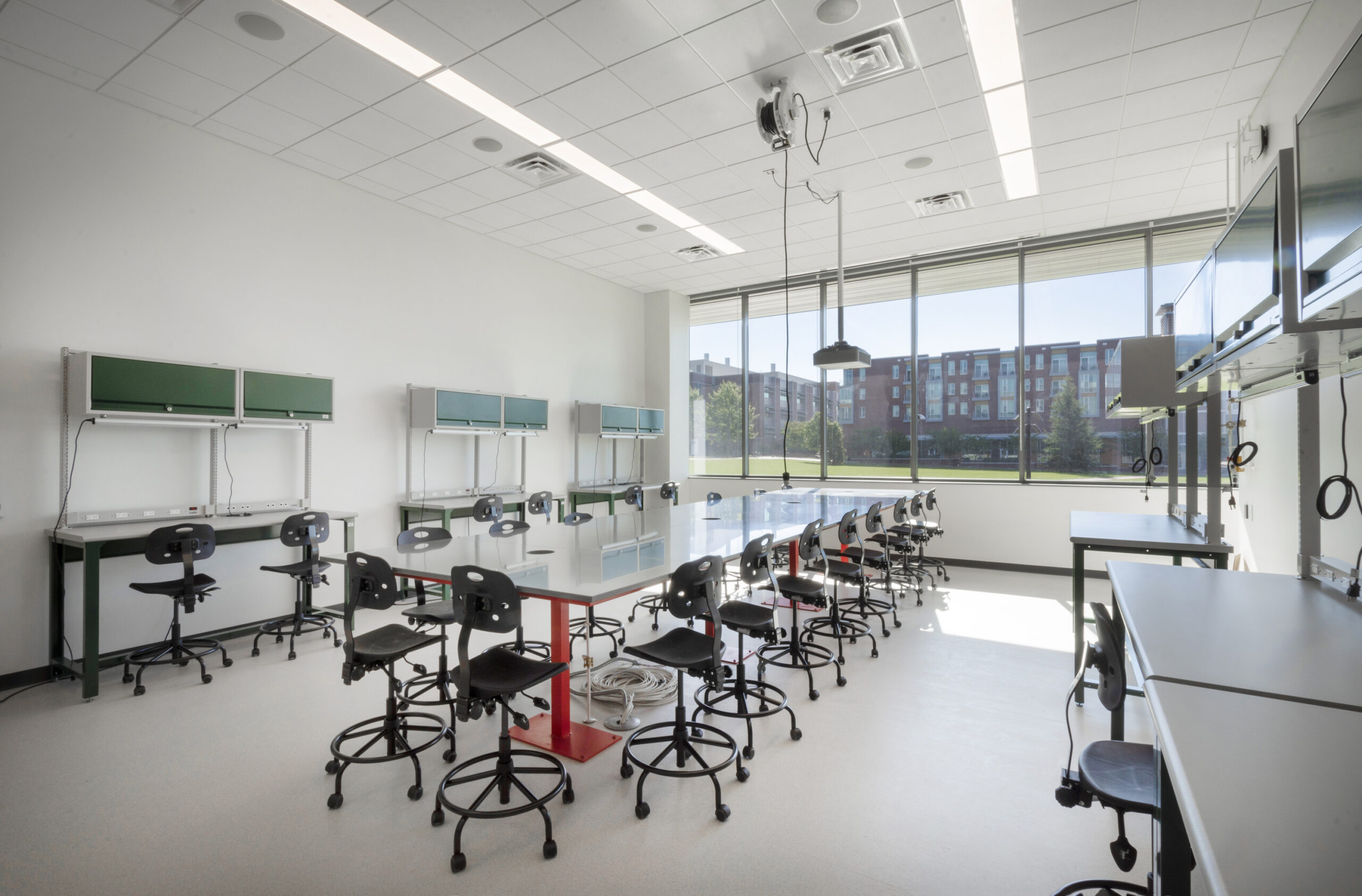
Each lab – such as Fitts-Woolard’s automation lab – had different requirements, resulting in close coordination with other disciplines during the design process.
On the surface, it’s easy to understand why a chemistry lab differs from a civil engineering lab. However, the reality is that even within a single discipline, like civil engineering, the labs can be very different. As a mechanical engineer, one of my roles on this project is researching industry standards and other guidelines to classify the labs. For example, the American Society of Heating, Refrigerating, and Air-Conditioning Engineers (ASHRAE) has certain lab ventilation design levels to help inform our design. The wet chemistry labs on the third floor had fume hoods, instruments on the bench tops, and other equipment. While the systems for these labs are comparable in complexity to the others, the requirements are much more straightforward and well-defined than the engineering labs on the first and second floors.
Coordinating with other disciplines early in the design process is vital in labs and engineering buildings like Fitts-Woolard. For example, lab buildings require taller above-ceiling plenum heights than others to accommodate mechanical systems and other systems requiring coordination – plumbing, electrical, structural, etc. By coordinating early, we can ensure that the floor-to-floor height meets requirements. Since this can impact the total height of the building and with mechanical spaces and rooms usually needing more space, we placed a large portion of the mechanical equipment on the roof, saving valuable interior space.
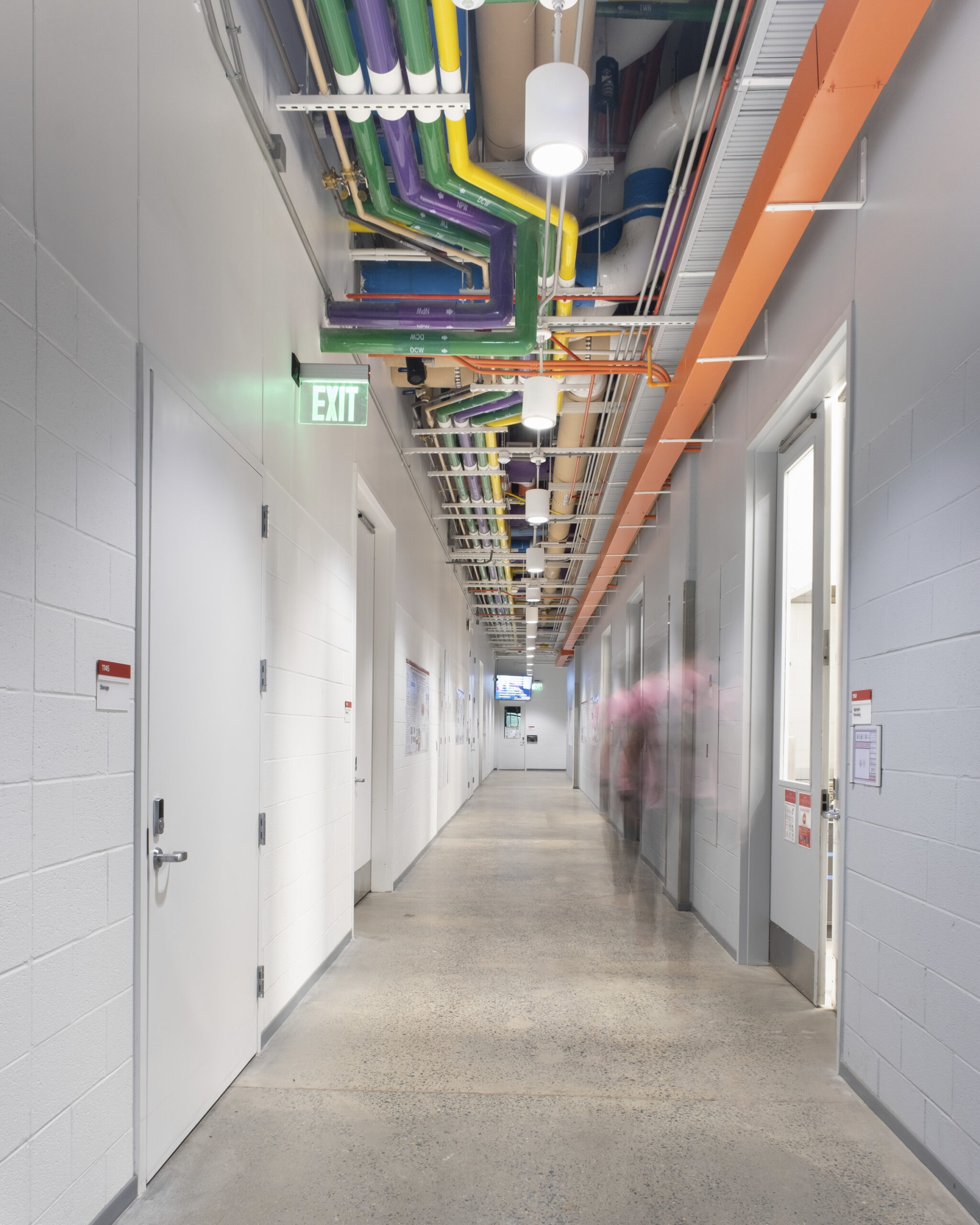
In keeping with Fitts-Woolard’s “on-display” theme, mechanical systems such as electrical, plumbing, HVAC, and fire-safety pipes are color coded, allowing them to be a teaching tool for students.
Building Out the Labs
Part of what made this project so seamless was that all major disciplines – architecture, engineering, and lab planning – were in-house. Since we were able to coordinate early, the project was indeed an integrated process. For example, the first floor of Fitts-Woolard is where we placed many of the “heavy” labs – a lot of civil engineering, concrete technology, aggregate, etc. Many of these labs create particulate that gets into the air stream, so we had to install a dust collection system that we designed to make sure those particulates weren’t recirculated within the building or adjacent labs. When dealing with particulates, it’s essential to capture contaminants at their source so they don’t harm occupants. The closer to the source you can catch any particulate, fumes, odors, or things like that, the less likely it is to bother adjacent spaces or cause more significant problems.
For single-pass labs in this building, where you’re not allowed to recirculate the airflow, we served those by a central air-handling unit on the roof. A fixed plate heat exchanger was used for exhaust air energy recovery to prevent any cross-contamination between airstreams, and high-plume laboratory exhaust fans were used to prevent re-entrainment.
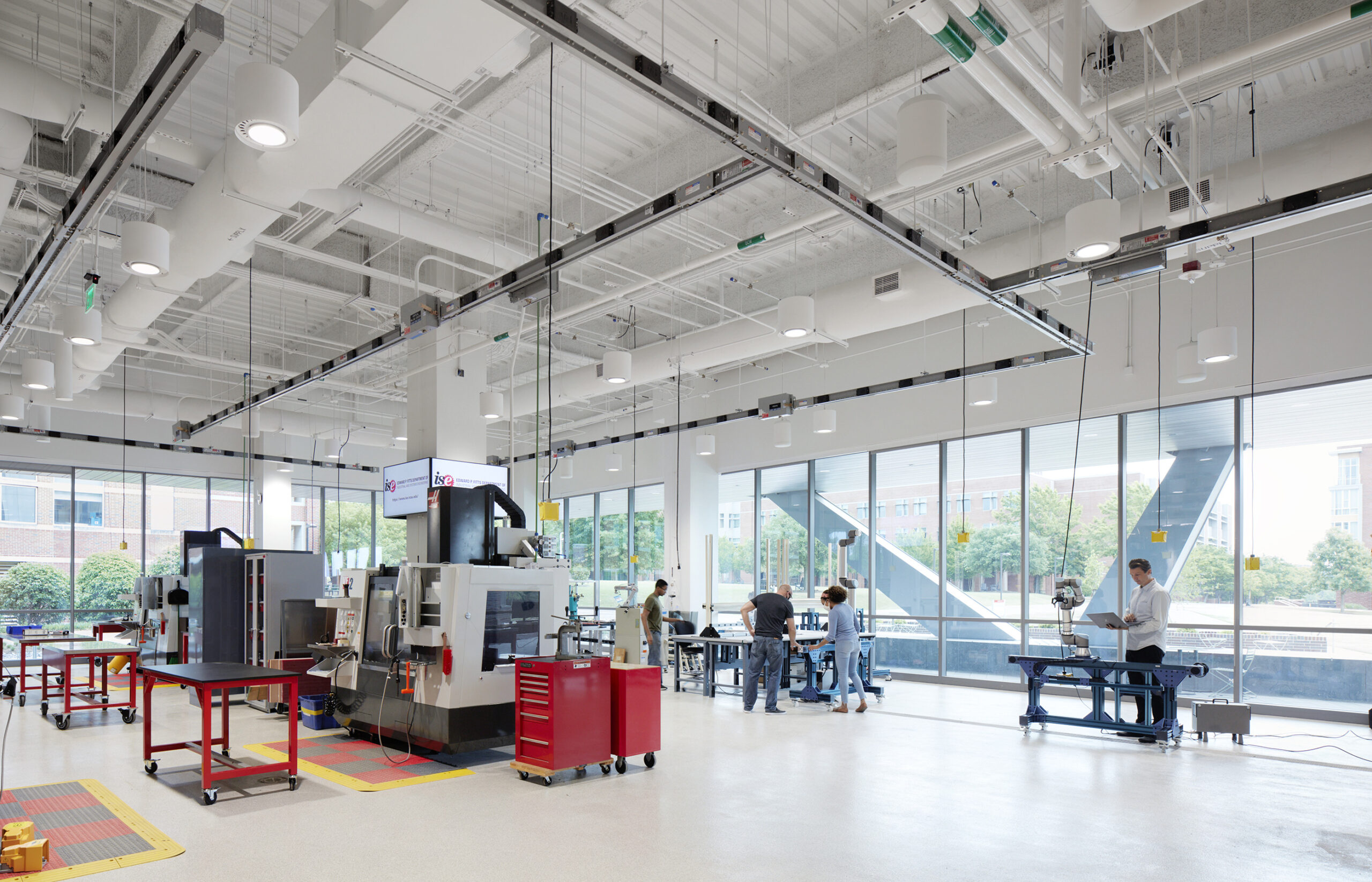
Located on the second floor, Fitts-Woolard’s advanced manufacturing lab had strict vibration, sound, and particulate requirements.
In addition to the work on the mechanical system – pressurization of the spaces, capturing fumes and particulate, air changes, and heat rejection – many labs also had strict vibration and sound requirements. For example, the second floor also houses the micro nano labs and advanced manufacturing labs, which contain machinery sensitive to vibrations. Working closely with structural engineering allowed us to design mechanical system accommodations for the structural slabs in these areas.
Another consideration is that some labs generate noise, and their adjacency to classrooms or offices could require sound dampening or mitigation. From a mechanical standpoint, if a fan or piece of equipment generates lots of noise, we may need to provide attenuation in the duct systems. A drywall can also help reduce sound in specific areas; sometimes, a double-wall insulated duct is sufficient. Once again, coordination with other disciplines – architecture, in this example – was invaluable.
Tips for Clients
It’s essential to think through the lab spaces – what are people going to be doing in them so we can accommodate their needs? One of the best ways to answer that question is to get feedback and insights from the end users, which allows us to pinpoint the type of lab that needs building and any specific needs the users and client may have.
The student project lab is a flexible space that supports student activities and storage for their work and projects. A good relationship with the client is also essential, accomplished with early and clear communication. Listening to their needs, suggestions, and concerns makes the project much easier for everyone involved. Good coordination with other disciplines is also crucial. In our case, almost everything was in-house, which was a significant advantage for this project.
Once you figure out what the requirements are and understand how those requirements impact the program and other disciplines, the project should be headed in a good direction.
Adam McElhaney, PE, is a mechanical engineer with more than ten years of experience designing HVAC systems for education and commercial projects. To learn more about HVAC design for complex lab buildings or to speak with Adam, please email amcelhaney@clarknexsen.com or call 757.455.5800.