Material Impact: How Clark Nexsen Can Source and Use Materials with Lower Embodied Carbon Emissions
Finding the right materials is a key process in many of our projects. New sustainability commitments, however, have placed a greater focus on how our firm sources and selects materials. In the following, Clark Nexsen sustainability student Erisa Harris shares details in her report on how to source popular materials, such as steel and concrete, that have lower embodied carbon and meet sustainability goals.
w
Why focus on embodied carbon?
The immediacy of the climate crisis demands swift, effective action from designers of built environments, which are responsible for around 40% of global carbon emissions. We are already taking giant steps in reducing operational carbon emissions by increasing the energy efficiency of buildings and electrifying our power systems. But what about the other side of the equation: embodied carbon, the global warming potential associated with building materials, construction, and demolition?
Unlike operational carbon, embodied carbon is an upfront cost that cannot be reduced over the life of a building through increased efficiency. It also encompasses a wide range of processes and systems. Through its entire life cycle—from material extraction to end-of-life demolition—a building touches nearly every major sector contributing to carbon emissions, and most of these life cycle stages are associated with the accumulation of embodied carbon.
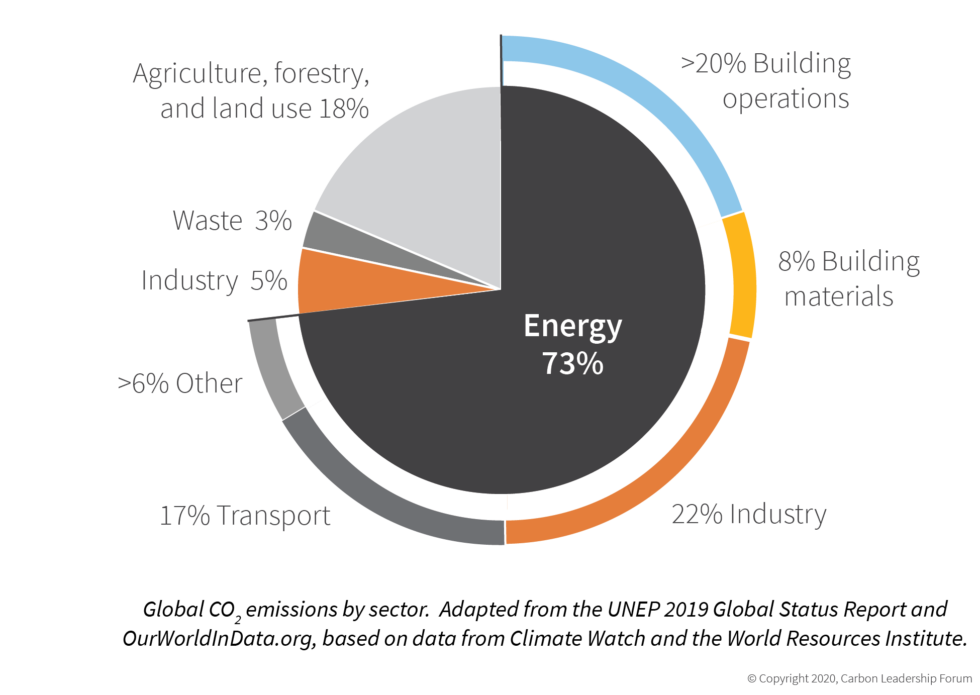
Image courtesy, Carbon Leadership Forum.
Overwhelming? Definitely. But as architects, engineers, and designers, this is an opportunity to quickly affect a wide range of sectors by creating a demand for responsibly sourced materials.
The first step in creating this demand is to ensure project teams are informed as early as possible about the factors going into a product’s carbon footprint, regardless of their familiarity with decarbonization. In producing reference documents, the objective was to create a comprehensive document that could function at multiple levels of depth: as a summary of actionable steps to reduce embodied carbon and as a collection of tools and datasets that could be used for further investigation by sustainability leaders within the company.
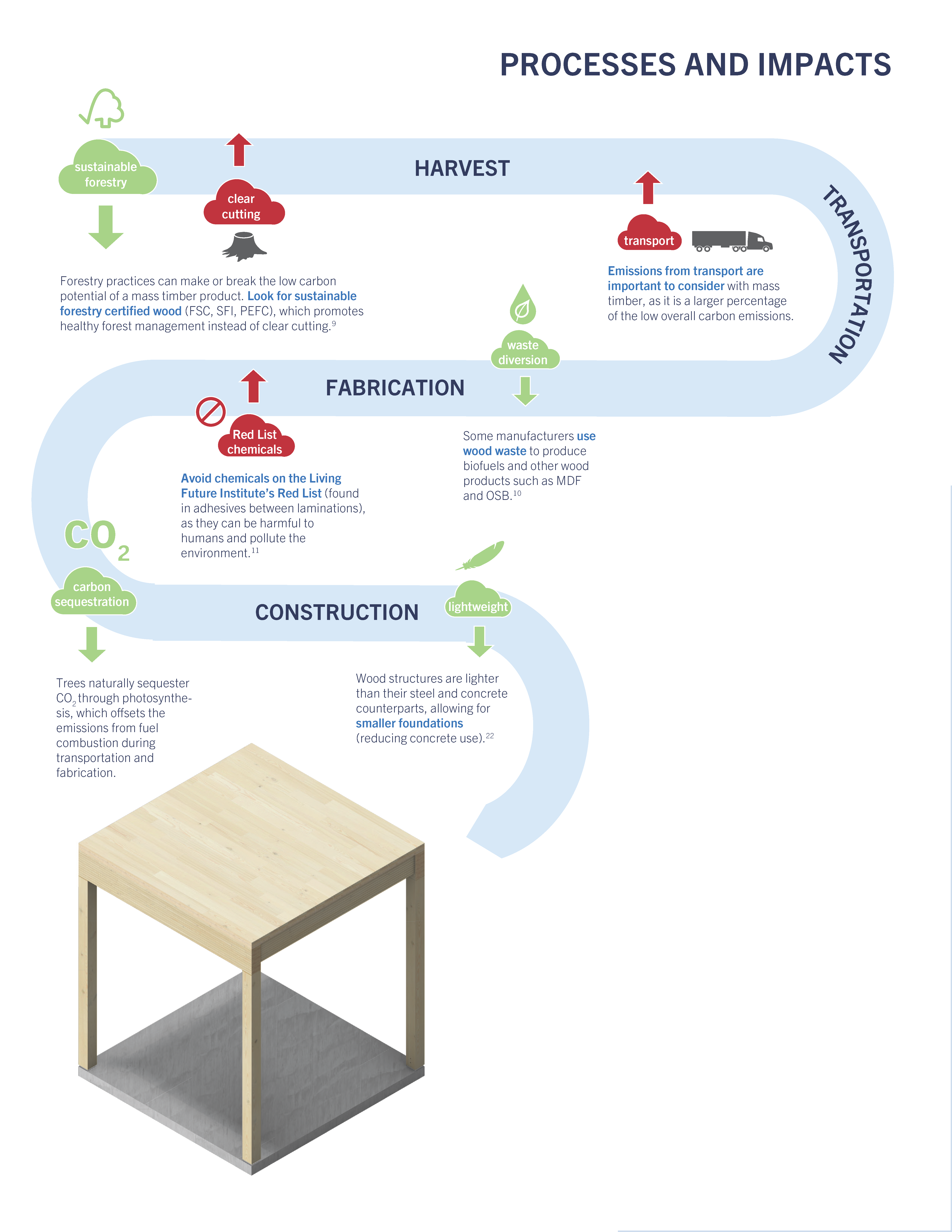
Prioritizing region
Why was it important that Clark Nexsen develop an internal document when many industry guides and tools for embodied carbon reduction already exist? Most existing guides paint with a broad brush to provide guidelines that apply to a wide range of designers, from those in the Pacific Northwest to the Southeast. This type of guidance makes it difficult to provide specific information about the resources available to particular regions, especially those not at the forefront of sustainable building.
Clark Nexsen works on projects throughout the United States and overseas. However, the firm decided to start with the regions where its offices are located. Looking at embodied carbon through a closer lens allowed for identifying regional priorities and evaluation of manufacturers that local contractors will order from.
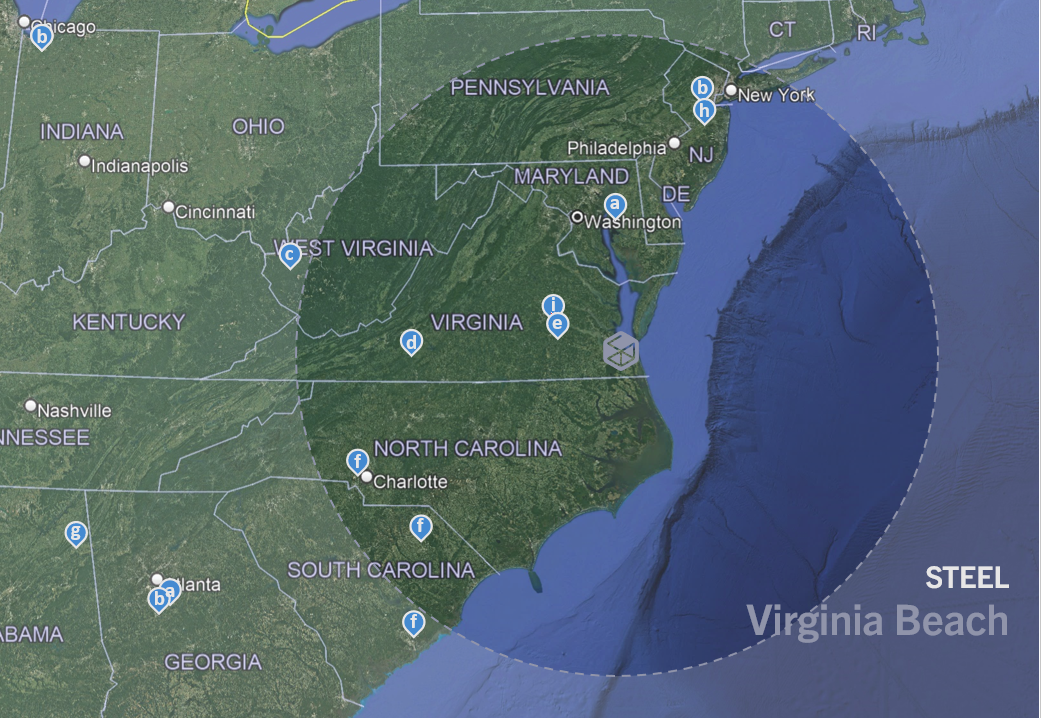
Transport of materials from manufacturing facilities to project sites was another factor that needed to be addressed as it related to Clark Nexsen’s carbon footprint. Though emissions from transport are often a fraction of the emissions associated with manufacturing a product, shipping over needlessly long distances should be avoided when possible. However, little data is available to determine exactly how much reducing transportation distance might impact the overall carbon emissions of a specific project.
Using fuel combustion data provided by the U.S. Environmental Protection Agency, emissions estimates were calculated for transporting material to selected Clark Nexsen offices as a jumping off point for visualizing the impacts of transportation on a project.
Key takeaways
The research focused on structural materials, as they comprise a large portion of the built environment and are associated with carbon-intensive processes. The following are key findings about these high-impact materials pertaining to regional manufacturers.
Concrete—a lost cause or an opportunity?
Concrete is ubiquitous in the built environment as the main component of building foundations and civil applications—at the same time, the manufacturing processes make it a material high in embodied carbon.
Producing portland cement, a key binder in today’s concrete, results in chemical reactions that release carbon. These reactions are the source of a large portion of concrete’s carbon emissions which cannot be avoided by switching to renewable energy. An effective way to reduce concrete’s embodied carbon is to reduce the volume of portland cement in a mix by replacing it with supplementary cementitious materials (SCMs).
SCMs such as fly ash and slag are widely available in the region, making mix design a priority in reducing embodied carbon. Many manufacturers also have carbon injection capabilities, a technology that improves concrete strength and sequesters carbon in the concrete. Our research revealed that manufacturers in Southeastern states perform better than the U.S. average in terms of reported global warming potential—landing in a similar ballpark to European concrete manufacturers.
The circular economy of steel
Steel is another carbon-intensive material that is virtually unavoidable in structural assemblies. Mining raw iron ore is destructive to the environment and surrounding communities, and melting the ore in a basic oxygen furnace (BOF) to produce steel requires high temperatures only achievable by burning fossil fuels.
The strength of steel lies in its ability to be continuously recycled without degrading its functional properties. Electric arc furnaces (EAF), which do not have the capacity to process raw iron ore, melt iron and steel scrap into new steel with high recycled content. Because these furnaces are powered by electrodes, they can also use renewable energy sources.
The U.S. has the largest ratio of EAF to BOF factories out of the major global steel producers, so buying domestic or local steel tackles the embodied carbon problem on two fronts—from the perspective of reducing emissions from transport and by increasing recycled content.
Despite ready access to steel with high recycled content, carbon footprints can vary widely between facilities, even under one regional manufacturer. For example, Nucor Berkeley, located in South Carolina, has nearly double the reported global warming potential as Nucor Yamato Steel in Arkansas. When determining a facility to buy from, it is essential to obtain facility-specific EPDs.
A caveat of EAF facilities is that they often lack the capacity to manufacture cold-formed shapes, so products such as light gauge steel framing and steel decking tend to have lower recycled content and, therefore, higher embodied carbon.
Mass timber on the rise
Mass timber construction has seen a surge in popularity in recent years, not only for its aesthetic and biophilic qualities but for its relatively low carbon footprint. In this enthusiasm, we must be aware that mass timber can have just as much embodied carbon as concrete or steel based on how source forests are managed. Forestry practices, overlooked in transparency documentation, such as EPDs, are linked to embodied carbon because they determine how much forest is left over to continue sequestering carbon after a timber harvest. To provide more transparency on this topic, the Forest Stewardship Council (FSC) certifies companies that promote healthy forest practices to its strict standards.
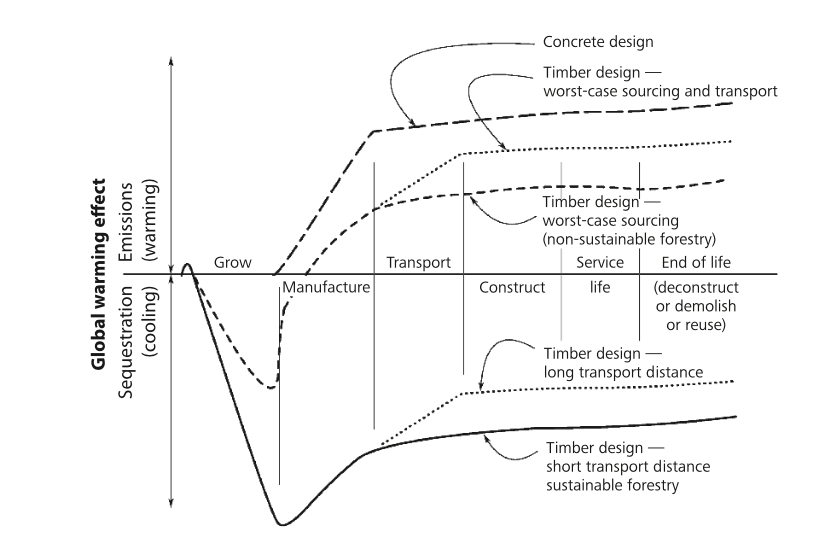
Image courtesy, Forest Stewardship Council.
Compiling region-specific data on mass timber manufacturers was a priority during the research process, as the Southeast U.S. has some catching up to do with the Pacific Northwest and Europe regarding the supply system and knowledge base.
However, there is encouraging growth in the mass timber industry on the East Coast. The number of fabricators in the area has nearly doubled in just the past four years, though many will still have to rely on nonlocal wood early on.
So, how do we ensure that the mass timber products we procure are locally and sustainably sourced?
- Getting an idea of where the wood was harvested is simpler than tracking down elusive supply chains—the species of wood used is often enough information to determine where it might grow. A good rule of thumb is to order products made from Southern Yellow Pine, which is native to the Southeast, as opposed to Douglas Fir, which grows primarily on the West Coast.
- Finding sustainably forested timber products is trickier, as the mass timber industry in the region is not yet robust enough for FSC certified glulam and CLT products to be commonplace. However, manufacturers may be certified by less prescriptive standards such as the Sustainable Forestry Initiative (SFI) and the Programme for the Endorsement of Forest Certification (PEFC), now accepted by both LEED and Green Globes.
Author
Erisa Harris is a Sustainabilty Research Student at Clark Nexsen for the summer of 2023, focusing on materials research.
Contributors
Adam Torrey, AIA, LFA, LEED AP BD+C, WELL AP, works across disciplines to bring analysis-driven perspectives to human-centered environments. He integrates passive and active sustainable design strategies, striving to combine design excellence with environmental performance. Adam leads Clark Nexsen's Embodied Carbon research team and currently serves on the AIA North Carolina COTE Leadership Group. To speak with Adam, please email atorrey@clarknexsen.com or call 757.455.5800.