Ospreys, Hangars, and PFAS: Implementing a Revolutionary, Environmentally Safe Fire Protection System for the U.S. Navy
Aiming to eliminate PFAS from their current fire protection system, the U.S. Navy was in need of a new system to protect its hangars, planes, and personnel from catastrophic events. In the following, Clark Nexsen senior project manager Brian Snyder highlights how collaboration and adaptability facilitated the timely implementation of an innovative and compliant fire protection system.
Clark Nexsen was tasked by our partners at Naval Facilities Engineering Systems Command Mid-Atlantic (NAVFAC MIDLANT) with the design and preparation of construction documents for a new MILCON project. The project design kicked off in the summer of 2021 with a straightforward objective. The CMV-22B Osprey squadron was moving to Naval Station Norfolk, and our team was charged with designing a new maintenance hangar and improving the surrounding apron and taxiways to support the mission. While many unique and complex design elements were associated with this facility, we will highlight the story of the fire protection system used to protect the open hangar space. Construction documents were completed by the fall of 2022, and the bid solicitation was anticipated for January 2023. In mid-December 2022, with winter holidays and end-of-year activities rapidly approaching, MIDLANT contacted us with a new project mandate.
It was reported the U.S. Navy elevated its urgency to move away from products and systems that contain per- and polyfluoroalkyl substances (PFAS). The established objective was to remove PFAS-containing elements from all designs by the end of 2023. To this point, the Navy had typically utilized aqueous film forming foam (AFFF) fire suppression systems to protect their hangars and similar facilities. Our design team was asked to explore an alternative to this traditional system, vet the reliability and constructability, and incorporate the new fire suppression system design into the construction documents before advertising the solicitation.
Several options were explored to replace AFFF, including a foam not containing PFAS, thus allowing the Navy to maintain the originally designed fire suppression system. Unfortunately, this technology was still in development, and the project required a system that could be immediately implemented.
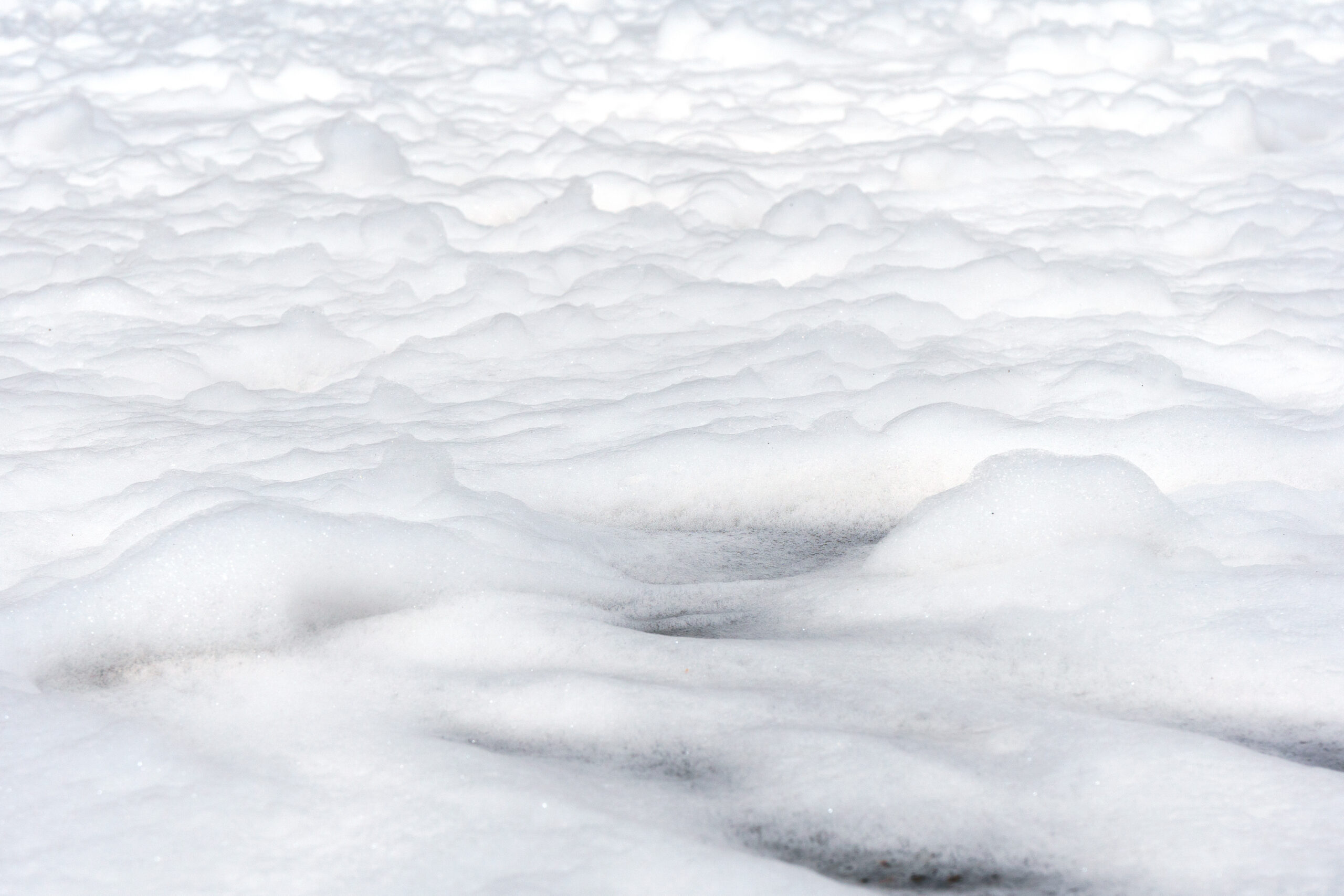
AFFF, used to fight fuel fires in aircraft hangars, contains PFAS, which has been shown to be toxic to the environment and human bodies.
Implementing a New System
The Navy pivoted to a new and unique system known as an ignitable liquid drainage floor assembly (ILDFA). ILDFA provides superior fire suppression performance and eliminates the toxic hazards of working with AFFF while meeting the needs of hangar operators, aircraft owners, insurers of all types, and local authorities. Manufactured by Safespill, the system is installed on the hangar floor and prevents the development of a pool fire by removing any ignitable liquid spills from the hangar bay into trenches using only water, a key environmental and operational advantage of the system. During a spill event, the fuel or other liquid flows into the hollow floor profiles through drain holes machined on the floor surface. Spill sensors in the flooring sections initiate the rinsing nozzles in that area of the hangar bay. The fluids are collected in a trench system and then disposed of before they can become a hazard.
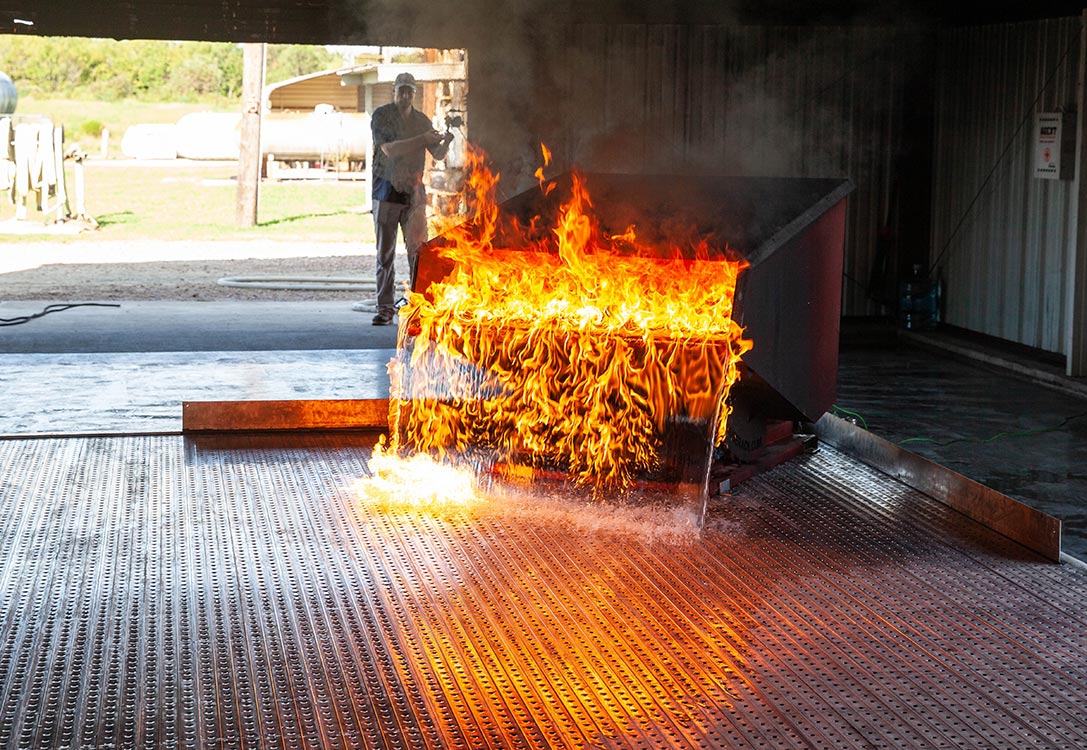
An example of the Safespill ILDFA system in action during a test simulating a dropped wing tank with 165 gallons of JP-4 on the floor. Courtesy, Safespill.
The timing of the redesign required the work to be done in an extremely short amount of time to minimize delays on the project’s solicitation date. Though a daunting challenge, the implementation was made significantly easier with the close collaboration of all project stakeholders. The ILDFA manufacturer, Safespill, was highly responsive to design team questions and quickly established themselves as invaluable project partners.
Safespill worked through their requirements, processes, and approvals before their involvement in this project, and implementation of their system within the hangar bay proved to be straightforward. The more complex design issue was working through the decision matrix of properly handling the water/fuel mixture as it leaves the hangar bay. With many perspectives to consider, a simple solution for one stakeholder could create an issue for another. The team reached a critical decision to separate the effluent from the sanitary and stormwater systems and to pump the effluent to a fuel-rated above-ground tank. This solution worked best as we could be confident all requirements were satisfied with the added benefit of avoiding a full environmental and stormwater review, which would not be accommodated within the framework of the current schedule. Other key decisions included spill reporting mechanisms, tank alarm levels, and notification triggers for base emergency services and maintenance teams.
The new approach to fire protection required Safespill to provide guidance and support to introduce this new fire suppression system to military personnel. The system was designed with user input, including hangar operators from the Navy and Air Force. This collaboration created more beneficial design aspects for operations beyond the benefits related to fire suppression. The floor system can contain and actively remove any liquid spills into a containment tank, allowing hangar operators to continue working without disruptions if a spill occurs. The system also includes foreign object damage (FOD) screens on the perforated drainage holes to prevent objects such as screws, nuts, and bolts from falling through the drainage holes of the flooring.
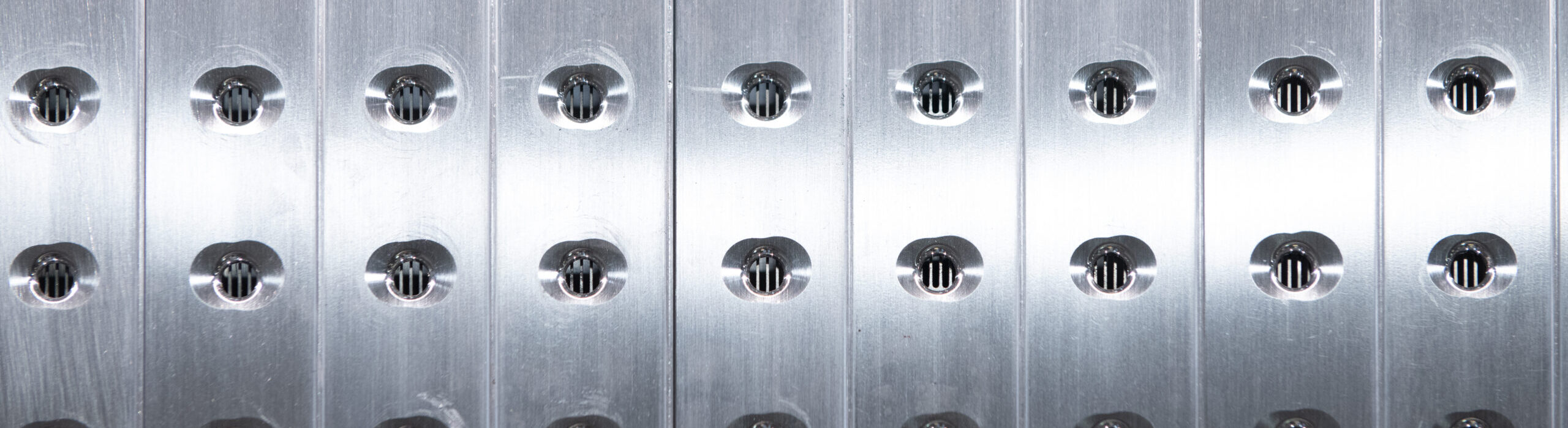
The holes of the Safespill floor have an aluminum-grade FOD screen to prevent small items from falling through. Courtesy, Safespill.
We discovered the importance of close coordination with the local environmental and utility-focused professionals during the ILDFA design process to understand the applicable and sometimes contradictory requirements, all of which were based on the previous mindset of hangar bay fire protection. We met with the Hampton Roads Sanitation Department to identify necessary permitting and the environmental effects of the new system. We tackled questions such as what happens if the tank fills up or there is an overflow? Where does the overflow go? How do these scenarios impact the environment? Ultimately, while these meetings slowed down the process, they resulted in solid and informed decisions and significantly increased stakeholder confidence and ultimate buy-in of all stakeholder groups, which was key to moving the redesign quickly forward.
Unsurprisingly, the most challenging aspect of the project was the schedule. Thanks to our team’s ability to accomplish almost every task in-house, we delivered our final design in just over a month. The convenience of collaborating with our own experts enabled us to move more quickly than most firms, which often employ outside consultants. Moreover, many of our employees have established lasting relationships with our NAVFAC counterparts and have built a level of trust that enables us to move efficiently through project milestones. This redesign effort included the typical technical team members from NAVFAC MIDLANT, Naval Station Norfolk, and Clark Nexsen. It also included an extended network of NAVFAC MIDLANT and LANT criteria and technical managers, Safespill technical staff, and local NAVFAC environmental, stormwater, and wastewater subject matter experts. Without concentrated effort, preparation, and participation in multiple weekly meetings by the project team, the redesign would have taken longer, and delays likely would have occurred.
Recommendations for Future Implementations
A fundamental and guiding principle at Clark Nexsen is building continuous improvement in our work. Our processes employ the concept of Kaizen, where we endeavor to build quality, honest assessment, and improvement in every step. Thus, following the successful completion of the redesign, our team performed a routine Project Retrospective to identify successes and weaknesses related to our project execution. In addition to typical discussion topics, the team focused on compiling a list of decisions and coordination items that could be developed to improve future designs. This list was provided to NAVFAC as a resource they could use to refine and provide solid design guidance moving forward.
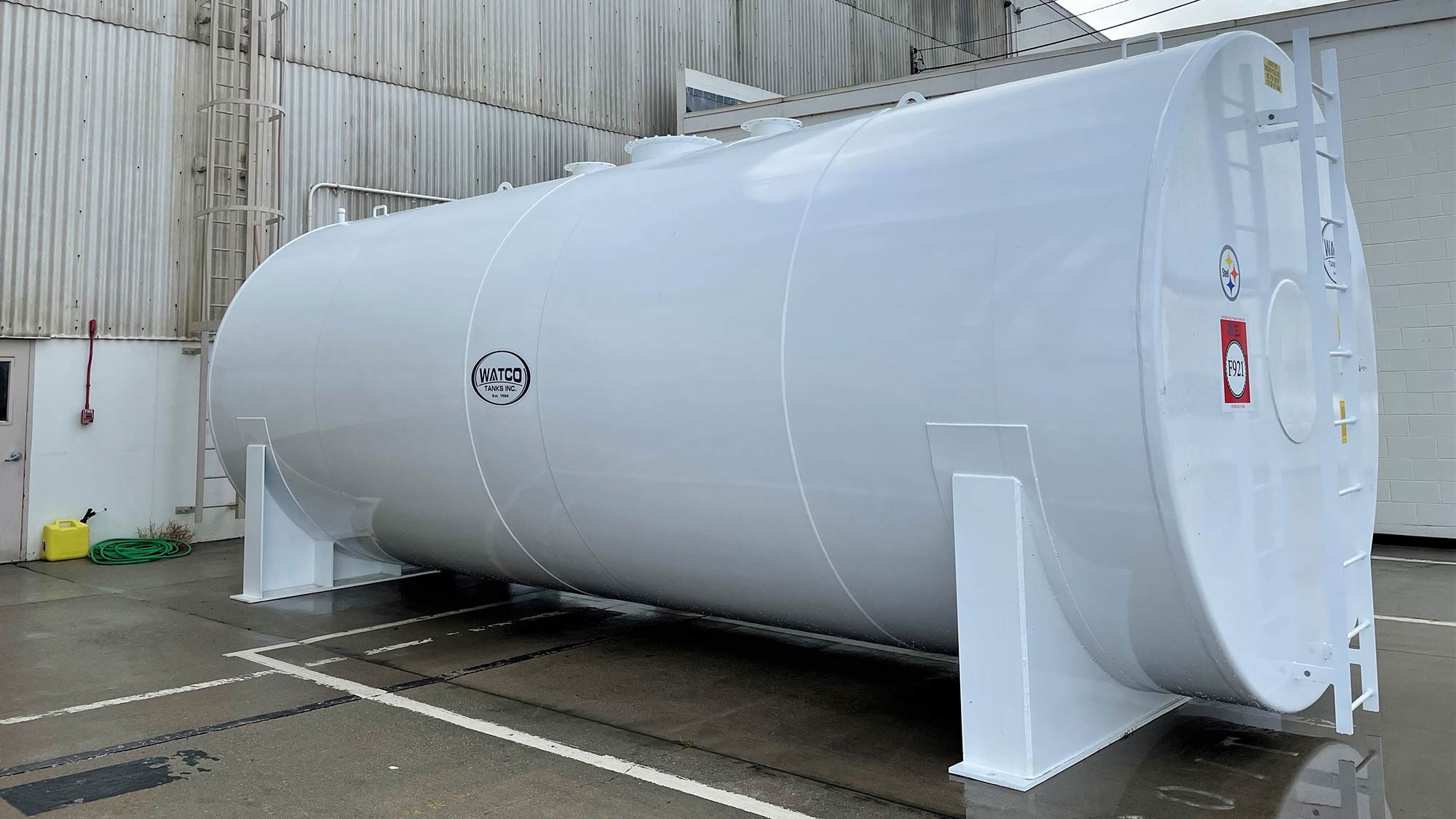
An example of a 15,000-gallon spill containment tank containing the spilled liquid and flushing water. Courtesy, Safespill.
Implementing a brand-new fire protection system for a multi-million-dollar military aircraft hangar is no easy feat, especially under the tightest time constraints. Thanks to our incredible partners at the U.S. Navy and Safespill, coupled with the unprecedented collaboration with local stakeholders and agencies, we were able to implement this incredibly innovative fire protection system effectively and quickly.
Clark Nexsen recognizes the significance and impact of the PFAS mandate on existing and future military facilities and stands ready to assist the government in finding innovative, agile, and cost-effective solutions for each unique situation. As the need to examine how the built environment contributes to the overall well-being of our society escalates, designers need to be ready to respond and partner with our clients and industry leaders to solve these complex challenges and continue to evolve our responses. We must implement innovation while never forgetting the criticality of the mission of the United States Department of Defense.
Brian Snyder, PE, is a Senior Project Manager and Associate Principal who leverages technology, open communication channels, and results-focused processes to manage federal projects for the firm. To learn more about this project or to speak with Brian, please email bsnyder@clarknexsen.com or call 757.455.5800.